ARC FLASH SAFETY PROCEDURES
You should make sure that you have detailed written and up to date safe working practices for people who carry out any work on or near low voltage electrical systems.
The HSE guidance note HSG85 Electricity at Work – Safe Working Practices is an excellently written and valuable resource in this respect. It clearly sets out decision-making flowcharts on whether to work live or dead and also gives some guidance on live working procedures.
There are many ways in which dangerous effects of electrical flashover can be eliminated or minimised some of which are detailed below. In the first instance there needs to be a risk assessment which will include an evaluation of the arc flash hazard. This can be carried out once a single line drawing of the LV mains distribution system and information is made available on the feeder cables as mentioned previously. The control measures follow a hierarchy with elimination being the first choice.
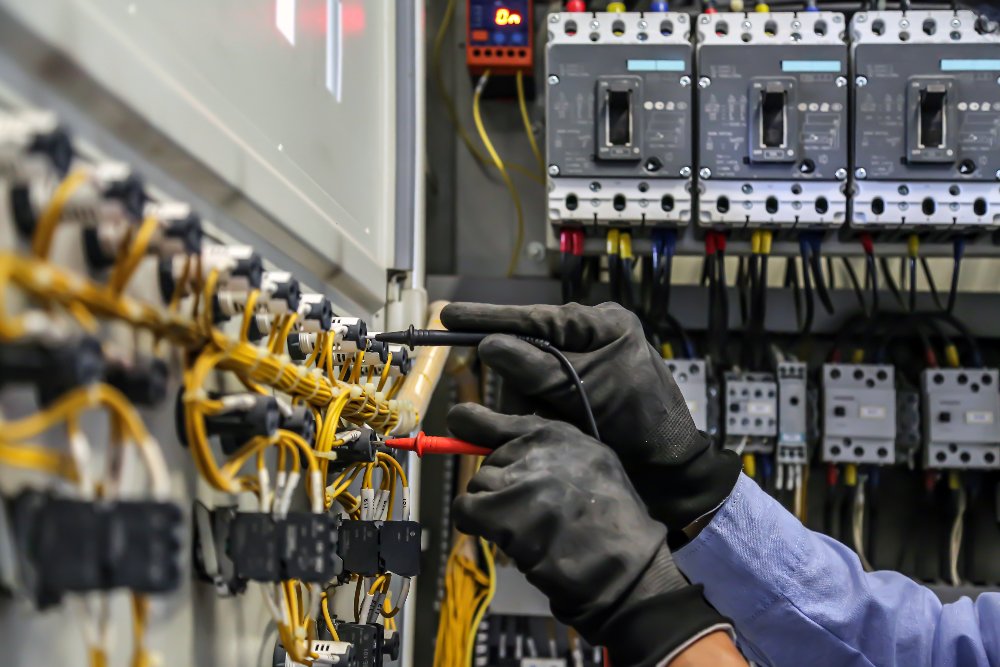
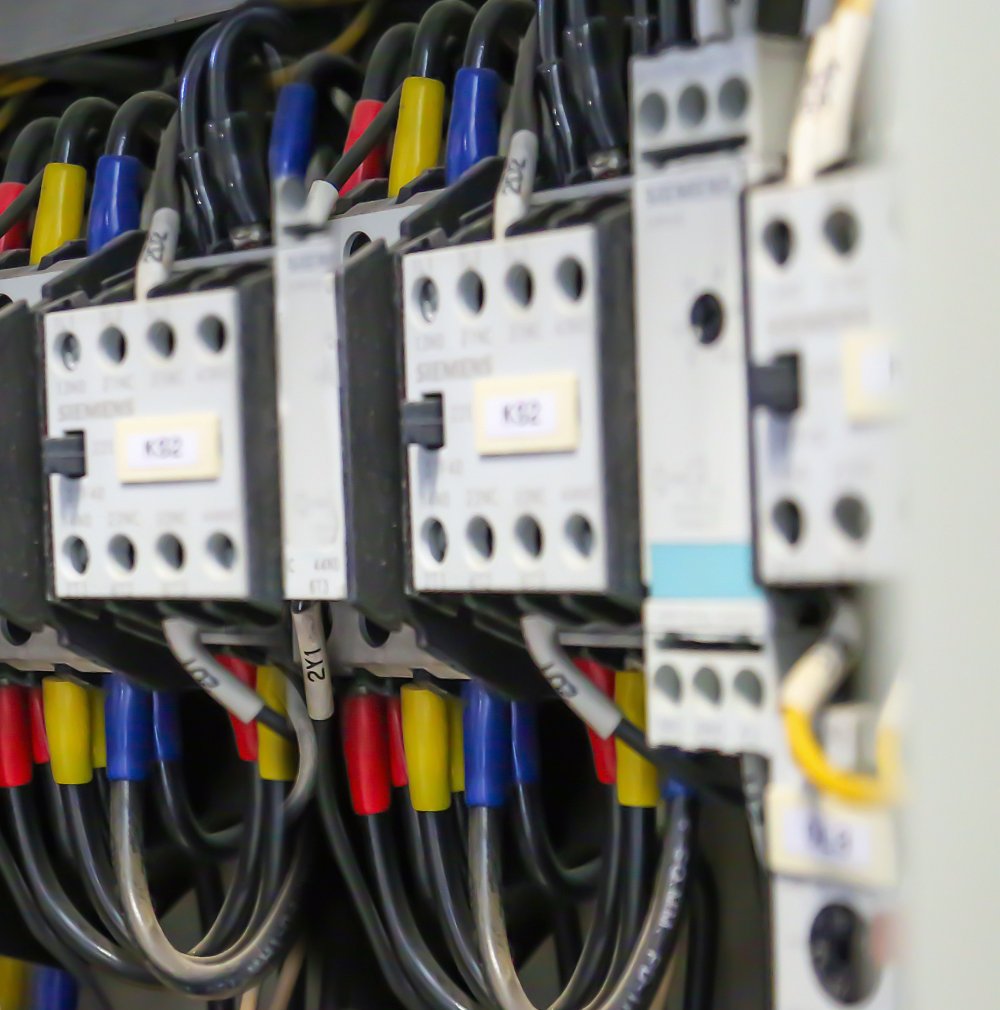
Elimination
The best way to prevent injuries from occurring is to de-energise equipment before beginning work.
Designers of electrical systems need to take into account the maintenance requirements with an objective of eliminating the need to work live at all in maintaining those systems. Some of the measures that can be employed are the segregation of power and control circuits, safe control voltages and currents, finger safe shrouding of terminals and built in test facilities. Even then, the specification and condition of the switchgear must be verified before work commences as things change. There are accidents where perfectly safe control panels have been rendered dangerous because electrical workers have not reinstated vital components such as door interlocks and insulating shielding on completion of work.
Minimisation
As the level of harm due to arc flash is a function of time exposure, minimisation may be achieved by looking at trip times or fuse ratings and exploring possibilities for faster disconnection times.
This may be a temporary measure for work on a particular piece of equipment by lowering the instantaneous protection settings to a minimum. There are possible engineered solutions such as retrofitting instantaneous trip devices for maintenance and there are even optical devices which detect electric arc in equipment providing automatic instantaneous trip of upstream switchgear.
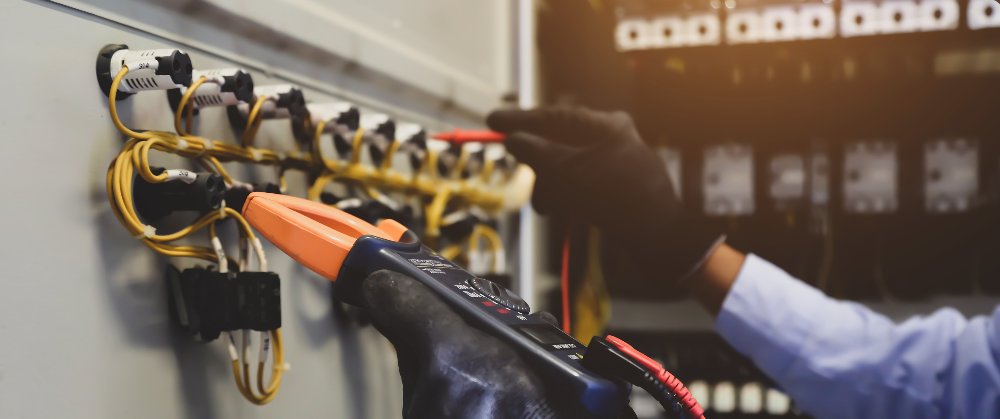
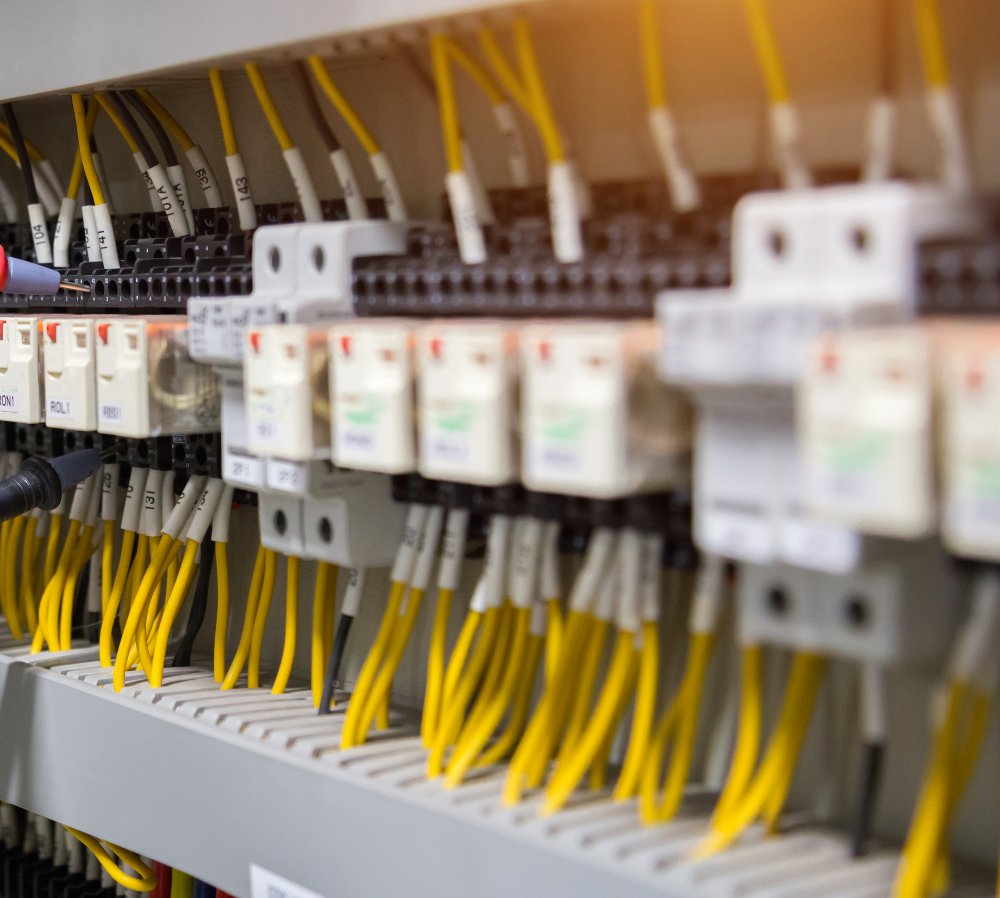
Information and Training
Electrical burns are very often quite horrific and can be sustained within a fraction of a second.
There is often a lack of understanding by electrical workers as to the nature of the hazard and the seriousness of the injuries that can be sustained in an electric arc accident which may go some way to explain why so many experienced personnel are involved in these types of accidents. Competent electrical workers should be trained in the decision-making process necessary to determine the degree and extent of the hazard and the PPE and job planning necessary to perform the task safely.
A review of electrical procedures and safe systems of work can raise the profile and understanding of the hazard and associated control measures. Where live working cannot be avoided then the safe working systems should stipulate the use of the correct equipment and instruments. Electrical flashover accidents are very often caused by the operator dropping un-insulated tools or metal parts or by using incorrectly specified instruments. There should be a rule that no live work will be allowed on equipment that is damaged even for the reasons of proving dead. There have been many incidents involving damaged cables where an approach has been made to prove dead when the damaged cable was in fact still live.
The US standard NFPA70E requires companies to place a warning label on electrical equipment likely to constitute an electrical safety hazard. The labelling gives information about the hazard as well as other control measures. Similar labelling techniques could be adopted but there needs also to be a verification process bearing in mind the earlier comments that things change. Be aware that the UK Health and Safety (Signs and Signals) Regulations 1996 defines the minimum requirements for the provision of health and/or safety signs at work.
Safety signs are to warn of any remaining significant risk or to instruct employees of the measures they must take in relation to these risks. It is very important that employees fully understand the meaning of such safety signs and are aware of the consequences of not following the warning or instruction given by the sign. It should be noted that arc flash labelling and field marking in Europe must conform to Directive 92/58/EEC and in fact labels based on the U.S. ANSI Z535 Standard would not be acceptable in most instances.
Maintenance of Equipment and Substations
An objective of maintenance procedures for electrical switchgear and equipment is that it will reliably and safely clear load and fault current and the associated protective relays operate within their design criteria. Contributory factors to arc flash incidents are often the presence of corrosion, dust, impurities, moisture and insulation failure. Other causes may be the entry into electrical equipment by rodents and birds. All of these factors should be included in maintenance programs.
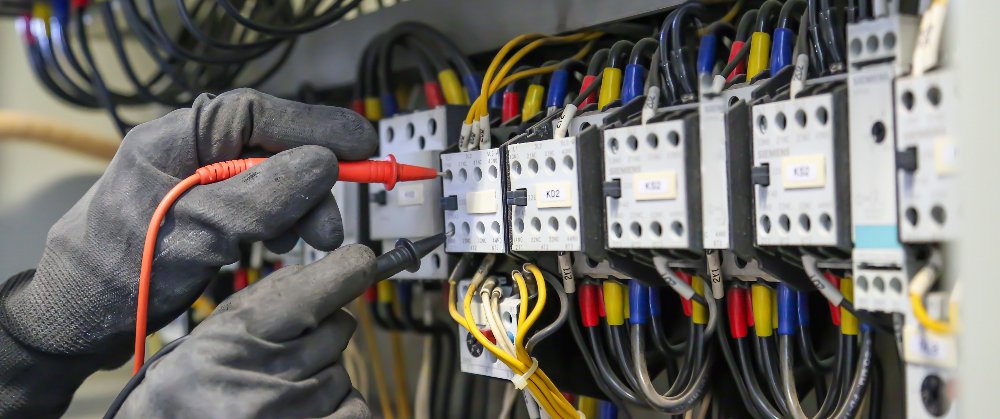
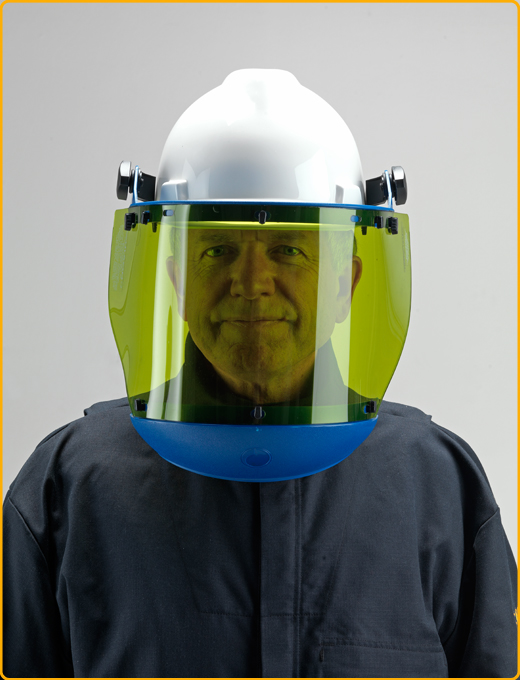
PPE
Arc flash clothing is designed to provide a barrier from heat and flame, to minimise total burn injury and to help provide the wearer with extra seconds of protection to help escape possible secondary explosions or fires in the work area. It can increase the chances of survival and decrease the need for medical treatment (skin grafts) and the chances of subsequent infections.
A compelling reason for electrical workers to be provided with fire retardant (FR) clothing is that ordinary clothes, especially synthetic fabrics (like nylon), may make injuries worse than if the skin was not covered at all. In an electric arc incident, denim jeans and jackets, cotton shirts, cotton/synthetic T-shirts, sweatshirts, fleeces or nylon jackets are fuel sources that ignite, burn and frequently melt onto the skin. The heavier the weight of the fabric, the more fuel there is to burn. While the explosion may be over in a fraction of a second, non-flame resistant clothing may keep burning; it takes just three seconds to sustain third degree burns.